As is often the case with large, complex systems that we don’t personally have the appropriate knowledge or training for, owners/operators, mangers, and regular staff of businesses that rely on refrigeration usually treat the equipment with an “out of sight, out of mind” or “as long as it’s running, it’s fine” mentality.
Without the necessary technical expertise to professionally diagnose a problem, they either pay the system little to no attention, or interact with it and don’t consider the consequences (because they’re not aware any exist). This can often lead to many expensive service calls or worse: an issue that can not only degrade the equipment but ruin it.
In this blog series—NRM’s Refrigeration Problem of the Week—we will take a look at real-world, sometimes very common, situations where having powerful control and monitoring tools averted disaster for a business.
This week’s problem: Compressor short-cycling in a quick-serve restaurant’s freezer
For our focus this week, we take a look at situation that one of our chain restaurant customers faced earlier this year.
This particular customer offers specialty-made sandwiches, burgers, desserts, and drinks. So, for them, any kind of issue has the potential to be a disaster with all of their ingredients being stored in their coolers and freezers. The success or failure of their business literally relies on their refrigeration system operating correctly.
But hourly employees and delivery drivers aren’t trained to look for things beyond whether the fans are running and moving the cold air around.
Short cycling is a common issue that often goes undetected because the system is running, and safe temperatures in the space are still maintained, but it’s excessively running much more than it needs to.
Imagine your car needs the engine to accelerate to 4000 RPM to maintain its speed up a steep hill. The engine does so and you successfully reach the top, back onto flat ground. At this point, your car is ready for the engine to decrease its RPM because you no longer need to accelerate, but instead it continues to rev up to 4000 over and over—dozens, if not hundreds, of times in quick succession.
Common sense would tell us this isn’t good for our engines. It’s the exact same for the compressors in commercial refrigeration systems.
The compressor circulates both refrigerant and oil through the refrigeration system, and very short runtimes can lead to oil pooling in the evaporator, instead of circulating back to the compressor.
If the compressors for this restaurant were to malfunction, all of their stored food could be at risk, and food safety is not a thing anyone takes lightly these days. Saying nothing for the thousands of dollars that would need to be sunk into an emergency maintenance call along with the cost of repair (or worse, equipment replacement).
In these screenshots, you can actually see when the compressor does the ‘engine revving’ of our earlier analogy. You can also see when the system calls for cooling but the cooling doesn’t initiate.
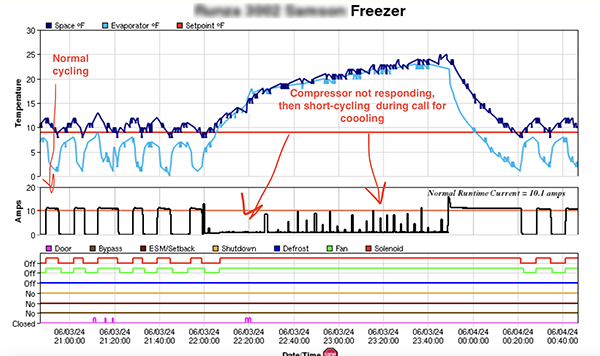
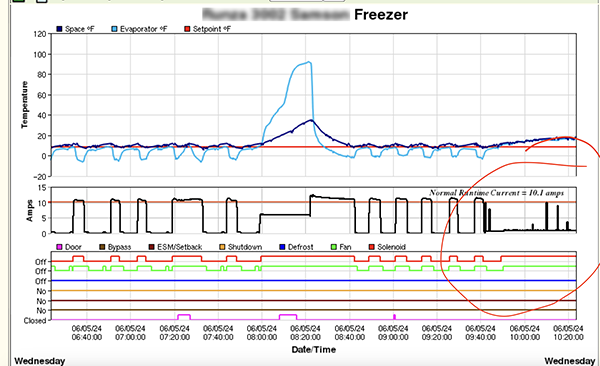
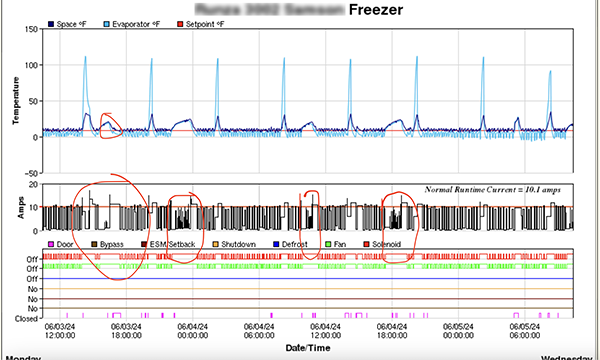
With NRM’s monitoring tools through our Remote Site Manager offering, this customer received an alert when the issue occurred (opposed to waiting for a high temperature), allowing them to get their refrigeration tech out to their site quickly.
These live visual diagnostics provide valuable context and information when the technicians are troubleshooting. A dedicated tech for the customer can even be added to the monitoring accounts to receive alerts directly.
Learn about all of the other ways Remote Site Manager can help you better protect both your vital equipment and valuable product with unique insights and a wealth of operational data here: Live Online Refrigeration Monitoring