Monitoring-Based Commissioning (MBCx) is getting a lot of attention these days in the energy efficiency field. Why? Simply put, to save money in energy usage and maintenance costs of HVAC, refrigeration, Chiller, and other types of equipment utilized by office, commercial, institutional and industrial buildings. For those of you who aren’t familiar with this term, MBCx is a combination of controls, sensors, software and sometimes ‘human review,’ that constantly monitors equipment by way of algorithms and real-time data to detect faults and optimize performance. To sum up MBCx with buzzwords, this type of commissioning fully utilizes ‘Big Data’ and the ‘Internet of Things’ to drive unmatched energy savings.
You may have also heard the terms Commissioning, Retro-Commissioning and Re-Commissioning. Let’s define these terms quickly before highlighting MBCx’s advantage over them:
- Commissioning – implies a one-time process of making sure the equipment is working properly at the time of the initial equipment installation.
- Retro-Commissioning – Commissioning the equipment ‘again’ after the first time. Implies a one-time deal.
- Re-commissioning – to commission the equipment yet another time.
You can probably already see the advantages of MBCx:
- MBCx offers permanent monitoring and analysis to ensure the persistence of savings achieved through operational and equipment improvements.
- MBCx can identify previously unrecognized and unquantifiable savings opportunities that are not otherwise apparent through utility bill analysis.
- MBCx allows you to constantly analyze all of your equipment 24/7, not just a few pieces of equipment at one moment or segment in time.
- Constant analysis of multiple pieces of equipment allows you to analyze trends and iterative effects.
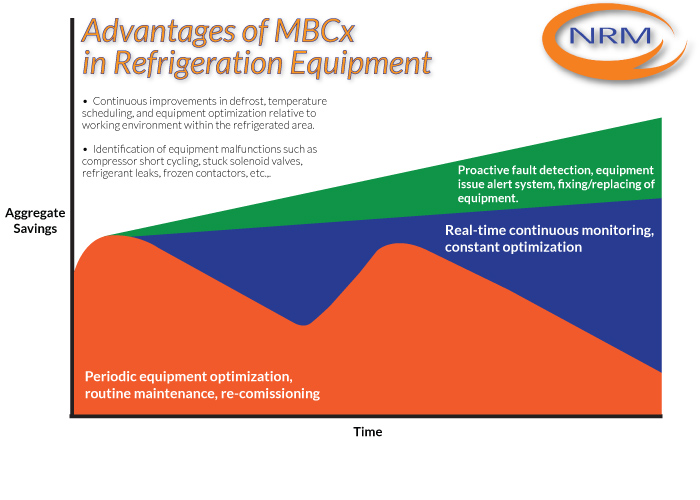
In fact, Lawrence Berkeley National Laboratory analyzed twenty-four test sites that implemented MBCx and found that the majority of systems had some form of energy-wasting deficiency that went unnoticed prior to the implementation. MBCx allows for immediate action to correct the issues.
“A total of 1120 deficiency-intervention combinations were identified in the course of commissioning the projects described in this report. The most common location of deficiencies was in HVAC equipment (65% of sites), followed by air-handling and distributions systems (59%), cooling plant (29%), heating plants (24%), and terminal units (24%). The most common interventions were adjusting set points, modifying sequences of operations, calibration, and various mechanical fixes (each done in about two-thirds of the sites).1”
The average savings against cost of implementation, as well as the average payback period, vaulted MBCx into its own stratosphere of energy efficiency measures.
“From these interventions flowed significant and highly cost-effective energy savings. For the MBCx cohort, source energy savings of 22 kBTU/sf-year (10%) were achieved, with a range of 2% to 25%. Median electricity savings were 1.9 kWh/sf-year (9%), with a range of 1% to 17%. Peak electrical demand savings were 0.2 W/sf-year (4%), with a range of 3% to 11%.1”
Most often, MBCx systems are cloud-based, which is ideal for modern equipment systems. In a nutshell, data is collected from various sources throughout the building and migrates to the cloud where it is continuously analyzed by pre-determined rules to identify specific faults. Ideally, this is an automated process where only the ‘exceptions’ are identified and then quantified as to the potential savings if they are fixed. Although IT security can be of concern, these issues are overcome through proper planning and communication when the system is set up.
Ensuring a harmonious relationship with IT and other software utilized in the building is but one hurdle in getting a MBCx system in place. It also requires full buy-in from the team (from shareholders to facility managers to engineers), and a company-wide focus on obtaining the most efficient operational capacity beyond simple energy savings. According to a Siemens report, the proactive upkeep of equipment is generally the toughest bridge to cross in reaching optimal performance.
“Through our experience over the years, we have come to understand that building maintenance is not always thoroughly completed for a variety of reasons, including, without limitation: the mechanical, electrical, and HVAC systems are considerably more complex than they once were; maintenance issues are resolved when the building is no longer comfortable and a tenant complains, or when a piece of equipment breaks and must be repaired or replaced; and because regular maintenance schedules (for example, filter replacements every six months) are not sufficient to support the building’s most effective performance. MBCx is a comprehensive business process to improve the way buildings are maintained by using technology as an enabler.
The results can include a lower likelihood of premature equipment failure; assistance with federal, state, local, and corporate requirements and regulations; energy and operational cost savings; and, finally, sustaining and perpetuating the improvements you have made.2”
As previously mentioned, there are many types of building operators that might be interested in MBCx. What types of equipment might be good to monitor? Well, all types – HVAC packages, VAV Boxes, Fan Powered Boxes, Air Handlers, Boilers, Chillers, Pumps, Cooling Towers and in our industry – Refrigeration!
Yes, refrigeration equipment such as walk-in coolers and freezers, and multi-deck and frozen cases, could also benefit by MBCx Systems. Why? Similar to equipment found in office and commercial buildings, refrigeration equipment could be operating inefficiently right under your nose and you don’t even know it. A 2006 Study from the Swedish Royal Institute of Technology supports this notion. They noted that of 164 refrigeration systems that were analyzed, 87% were operating with faults. After looking at various COP’s vs normal, they concluded that 15.8% of the energy costs associated with commercial refrigeration equipment may be waste due to poorly-operating equipment, even in systems that were recently serviced.
Some of you reading this may say “well, I have temperature alarms already in my refrigerated space,” BUT you would have no idea if one of those compressors had a short cycling problem (Compressor Short Cycling: A Hard-to-Find Energy Waster). Think about it another way – one of your car’s tires might have low-tire pressure, but you can still drive it. The issue is that you’re going to end up wearing it out sooner, and your Miles per Gallon won’t be as good as if all four tires were inflated to the recommended pressures. That’s why we love a car dashboard that will let us know when we’ve got low-tire pressure. That’s exactly what an MBCx system will do for your refrigeration equipment.
If you’re trying to decide if an MBCx system is right for you, the decision typically centers on the costs of implementing an MBCx system and the potential benefits versus the cost of doing nothing. Through your own due diligence or bringing in an expert like an energy consultant, you should start by trying to quantify the following:
- How much of electric bill is attributable to use of my refrigeration equipment?
- How much money am I spending on my electric bill that I might potentially save?
- How much am I spending on maintenance or repairs that I might be able to save?
Once you’ve quantified the potential savings, you can compare that against the costs of implementing an MBCx system to come up with a Return on Investment. You’ll then have a better handle of if you should move forward or not.
“We observed a range of normalized costs from $0.37 to 1.62/sf, with a median value of $1.00/sf for buildings that implemented MBCx projects. Per the program design, monitoring costs as a percentage of total costs are significantly higher in MBCx projects (median value 40%) than typical commissioning projects included in the Meta-analysis (median value of 2% in the commissioning database). Half of the projects were in buildings containing complex and energy-intensive laboratory space, with higher associated costs. Median energy cost savings were $0.25/sf-year, for a median simple payback time of 2.5 years. Significant and cost-effective energy savings were thus obtained.1”
Also, remember to check with your local utility to see if the costs of implementing the MBCx system can be offset by incentives or rebates. Some utilities will offer incentives on an ongoing basis for faults that are detected and fixed.
Our experience shows that refrigerated warehouses, wholesale warehouses, and distribution and processing facilities are ideal for a MBCx system. Refrigeration equipment, because it’s such an integral piece of the facility relative to lighting, HVAC and other energy-consuming equipment, can account for as much as 70% of the electric bill. So if you apply some of the statistics from the Swedish study above, that’s some real savings you could add back to your bottom line.